If your organization is in the business of owning, operating, maintaining and replacing assets of any kind – from trees, properties, vehicles, plant and equipment – you know that effective and pro-active maintenance scheduling, tracking and reporting is key to keeping your assets operational and in working condition. Down time is the enemy of productivity and profitability, being able to predict and prevent it is critical.
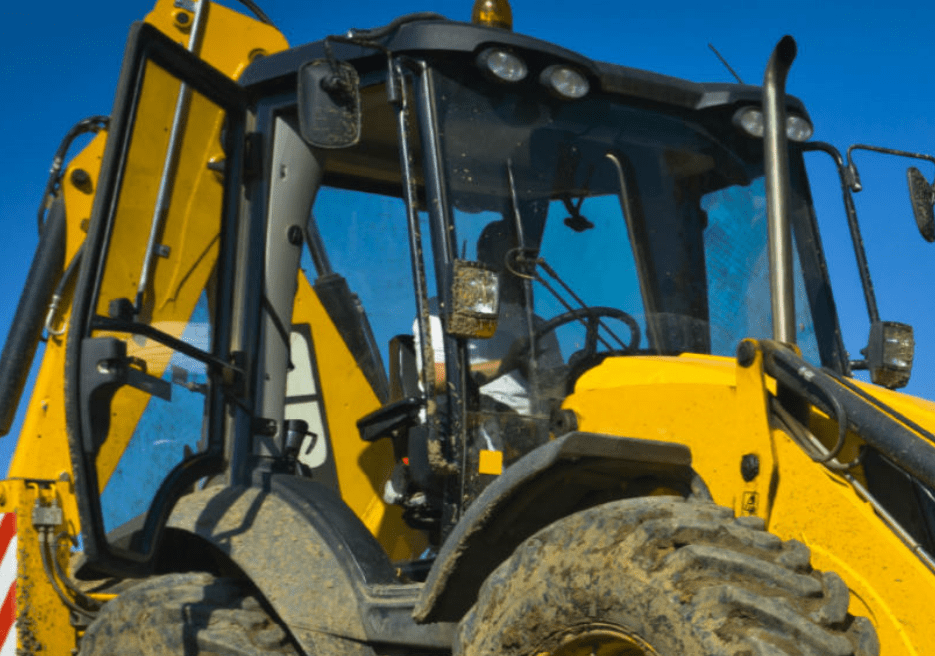
How does Enterprise Asset Management benefit your organization?
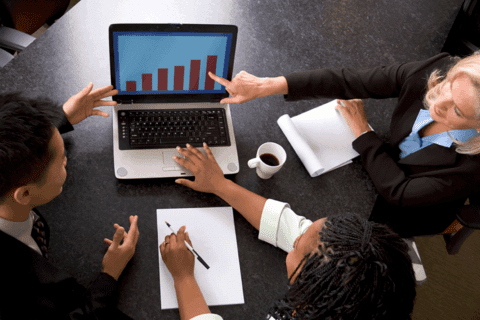
A good Enterprise Asset Management solution will help you:
- Reduce maintenance overtime, labor, and contractor costs
- Reduce maintenance material costs
- Reduce in production downtime
- Reduce new equipment costs
- Increase warranty cost recovery
- Reduce purchasing process costs
Features include:
Advanced Cost Control
For all assets, the costs including labor, expenses and spare parts are tracked and timestamped giving a complete view of the Total Cost of Assets (TCA). The TCA overview is available at the lowest component level as well as at a site, production line or machine level.
Corrective Maintenance
Corrective maintenance is carried out after failure detection and is aimed at restoring an asset to a condition in which it can perform its intended function.
Condition Based Maintenance
Condition-based maintenance (CBM) is maintenance performed after one or more indicators show that equipment is going to fail or that equipment performance is deteriorating.
Preventive Maintenance
Preventive Maintenance is supported through maintenance sequences, which can be calendar based (date, time, day, etc.), counter based (produced units, hours, miles, etc.) or condition based.
Predictive Maintenance
Asset counters can be defined for individual asset types and then updated either manually or automatically through e.g. direct integration to PLC’s. These counters are obvious candidates for predictive maintenance, where predictive maintenance covers advanced statistical analysis of one of more mathematical models underlying a given counter.